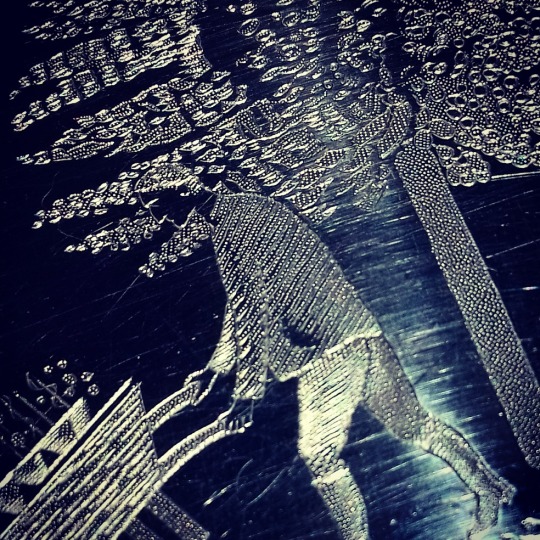
One of the items I own is an original engraving plate for Wedgwood by Eric Ravilious. I bought it as I like the social history of printed china, not only of Wedgwood, but when artists would design domestic tableware. Being a printing plate it is as close to the original drawings by the artist, but very few have survived (maybe ten) and most of them were melted down after the production ended.
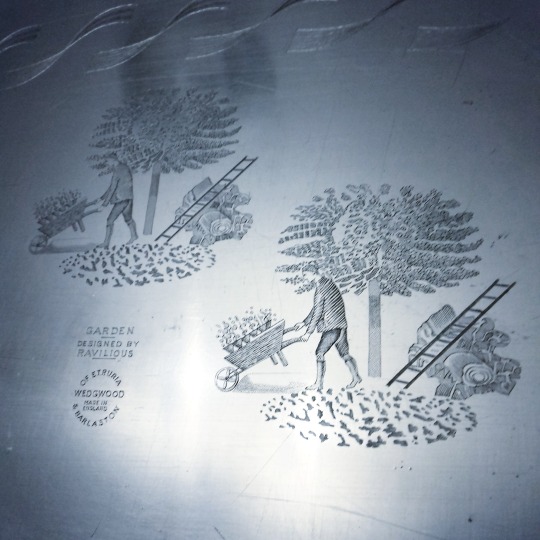
Metal engraved plate with the Ravilous design for ‘Garden’. From my collection.
Below is a printing taken from the plate, printed in black on to white paper.
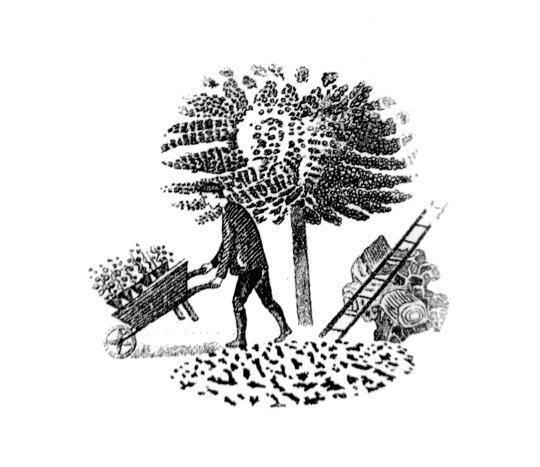
‘Garden’, the most elaborate of the designs (comprising a border, then vignettes and many smaller details from these), appears in the Wedgwood estimate books between November 1938 and May 1939. ‘Speaking for myself,’ Tom Wedgwood wrote acknowledging the receipt of some drawings, ‘I am delighted with them, particularly the Garden pattern; you must have put in a tremendous lot of work on these patterns since you were down here, and I do think you are to be congratulated on the result. †
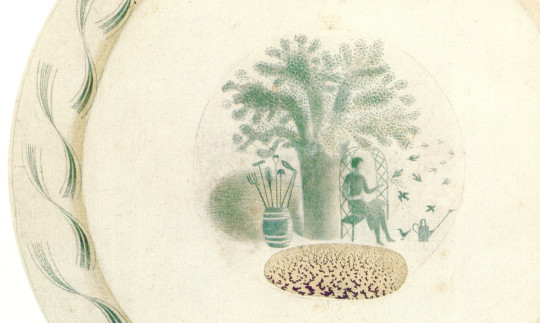
Detail: A collage of pieces making the finished plate by Ravilious.
The garden series had various vignette designs for the china pieces. Ravilious would paint them in with watercolour, pen and pencil.
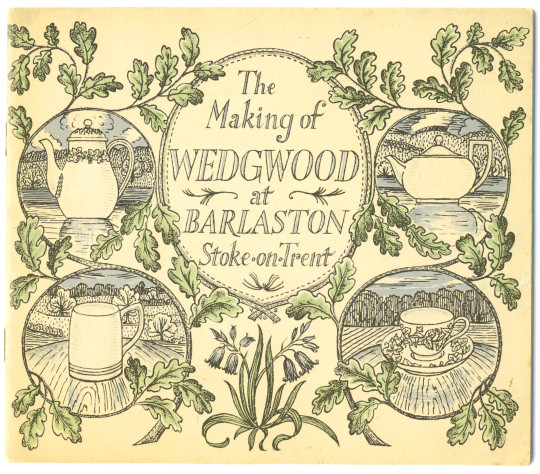
Below I have put more information from the Wedgwood guide to how the factory produced, printed and made the ceramics with the metal plates. ‡
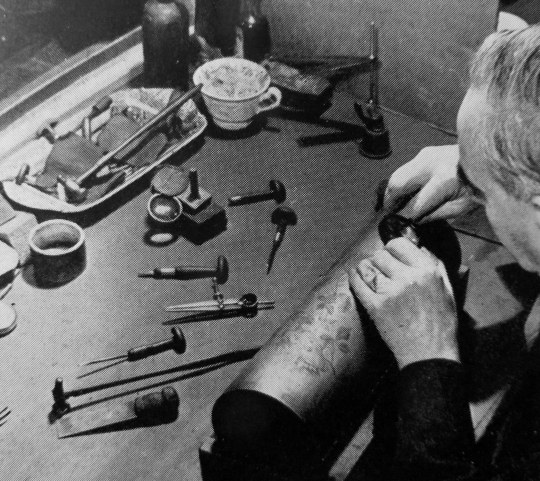
The Engraver:
A pattern which is designed for reproduction by printing is first drawn to fit the curves of the various pieces of ware (china) to the width it will be applied. It is then engraved either on a flat copper plate or on a copper cylinder. This is done with a sharp pointed tool called a “graver”. Light and shade effects are obtained by minutely graduated punched dots. This craftsmanship calls for the highest degree of skill which can only be acquired after many years of experience.
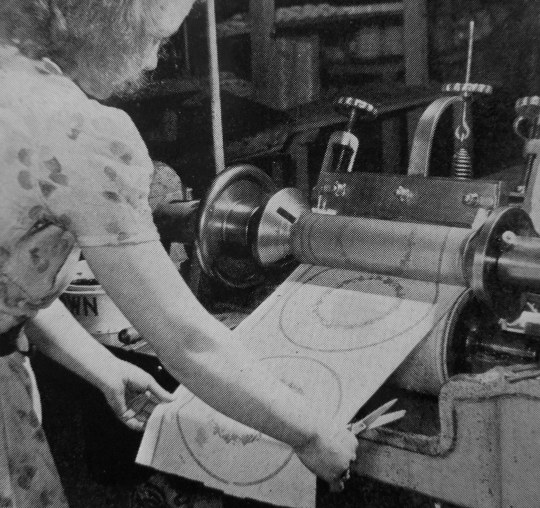
The Printer:
Prints can be taken of flat copper plates by hand. The heat softened colour is rubbed into the engraved lines and the print is taken off on to specially prepared tissue paper by dressing the copper plate with the tissue paper between two flannel covered rollers. Nowadays, power operated printing machines are employed. The engraved copper cylinder prints the pattern on a continuous roll of paper. The colour mixed with oil is fed to the cylinder which is heated by an electric element in its centre.
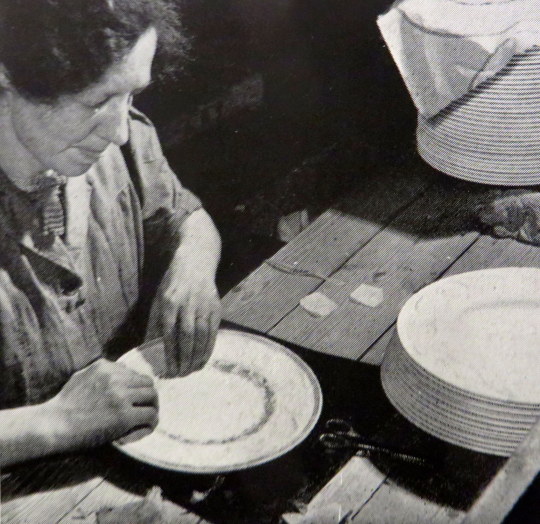
The Transferrer:
All superfluous tissue paper having been cut away the transferrer applies the paper print. It is vigorously rubbed on to the ware first with a flannel and then with a hard brush to ensure that it adheres firmly and evenly. Afterwards the paper is washed off leaving the pattern transferred to the ware. This is then passed through an electric kiln to harden on the colour of patterns printed on biscuit or to fuse the colour to the glaze in the case of those printed on the glaze.
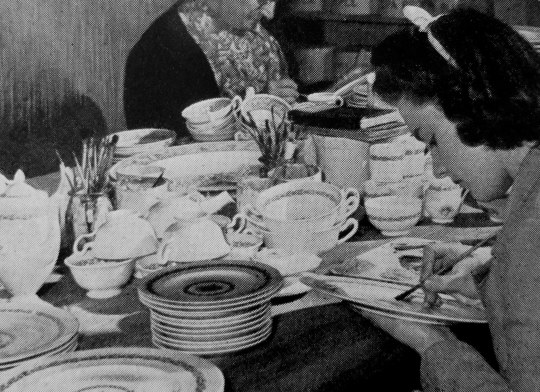
The Enameller:
Printed patterns can be enriched by the addition of ceramic colours, the painting of which calls for great skill.
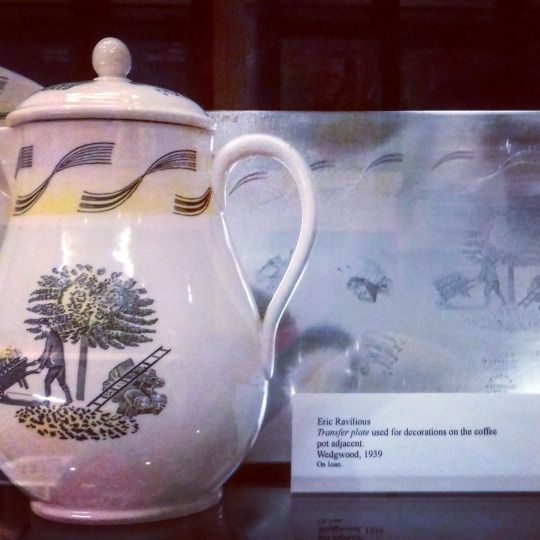
† Ravilious & Wedgwood: The Complete Wedgwood Designs of Eric Ravilious by Eric Ravilious and Robert Harling, 1995.
‡ The Making of Wedgwood at Barlaston, Stoke on Trent.