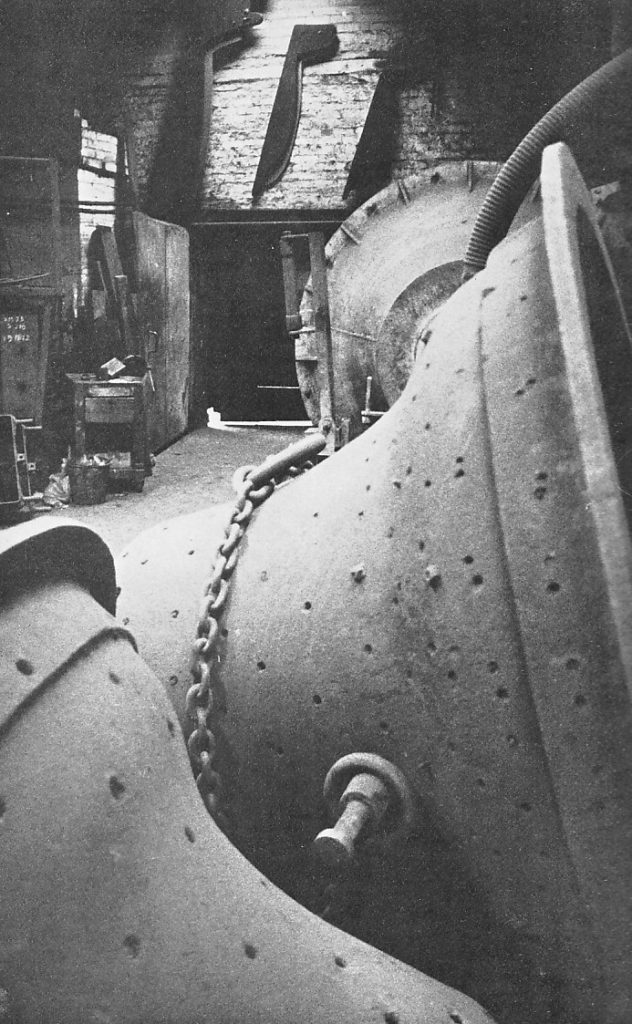
In AD 945 the Abbot of Croyland had a great bell cast, which he called Guthlac, after the abbey’s founder. Egelric, his successor, added six more bells, called Bartholomew, Betelin, Turketil, Tatwin, Pega and Bega. Perhaps these were saints’ names, though some of them have a suspiciously pagan ring; one suspects though, that pious dedications cloaked a natural human instinct to give personalities to objects whose individual voices had so distinct an identity. It was not until the sixteenth century that the name of the bell founder himself began to appear on the bell, and it was a sixteenth century founder, Robert Mot, who opened the foundry in the Whitechapel Road. Two of the bells of Westminster Abbey bear his name and the rest have also been made or recast at Whitechapel. Indeed, many of his bells are still in use and frequently return to the Whitechapel Foundry for repair or rehanging. And the methods used for the casting of bells have changed little since Mot himself made them.
In 1738 the foundry moved across the road and took over the site of a coaching inn called the Artichoke. A remaining area of the old courtyard is still the centre of today’s complex of buildings (fragments of saltglaze bellarmine bottles still turn up). Here Big Ben was cast in 1858, only one of many famous bells that have issued from the foundry. The bell moulder at the time, Thomas Kimber, also kept records of the details and inscriptions of every bell that came into the foundry and it was from his drawings that the foundry was able to remake many bells which were destroyed during the Second World War.
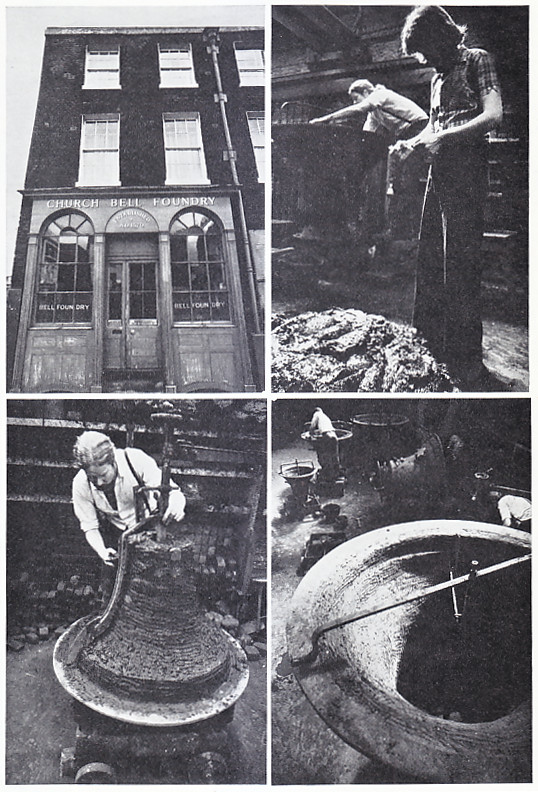
Bells are commonly associated with change ringing, in which intricate patterns of sound are made by varying the order in which the bells are rung. The practice was introduced in England at the beginning of the seventeenth century and presupposes a set of bells of varying sizes, to give the different notes, The bells are swung by ropes on the frame on which they hang, so that the whole bell is turned through a full circle, and struck one blow by the clapper. This method of ringing gives a full deep tone, and naturally superseded the previous one in which the clapper was itself attached to the rope and so pulled against the bell.
The characteristic bell shape evolved during the Middle Ages. The bell grew longer, and the flared lip developed, with a soundbow, or extra thickness, at the point where the clapper strikes. Both these developments went to make better sounds, but an important advance came in the seventeenth century when (two Dutchmen, the _ brothers Hemony, learnt to adjust the harmonics of the bell, and to grade correctly not only the note heard when the bell first sounds, the “strike”, but the other notes which follow as the sound vibrates, the “hum”, which should be one octave below the strike, the partial tones in between, the minor third and the fifth, and the octave above the strike. The results of their experiments were lost however, and harmonics remained largely a matter of luck until they were rediscovered at the end of the nineteenth century.
To begin the actual making of a bell is a messy business. To build up the “‘core’”’, the mould on which the inner shape of the bell is formed, a mudbath of London clay, horsedung and horsehair is stirred in the middle of the floor and when the mixture is of the right consistency it is plastered by hand onto a layer of bricks. The shape is checked against a moulding board, which represents the exact dimensions of the inner curve of the bell. When finished, the mould is dried in an oven and coated with graphite and polished for a very smooth finish. A similar process is used to make the “cope”, the outside shape of the bell, which is built up inside an iron case. It is finished m the same way, but before dry ng any inscription is pressed to the damp loam so that it stands out in relief when the bell is cast.
Next comes the process of “closing down”. The cope is lowered over the core and the two moulds are firmly clamped together. A huge ladle is filled with molten metal from the furnace — approximately 77 per cent copper and 23 per cent tin – and this is poured into the space between the cope and the core. The metal must be at exactly the right temperature; small bells needing a higher temperature than large ones. Slowly the bell cools, taking between one and eight days, according to size. Finally the moulds are chipped off and the bell is ready for tuning.
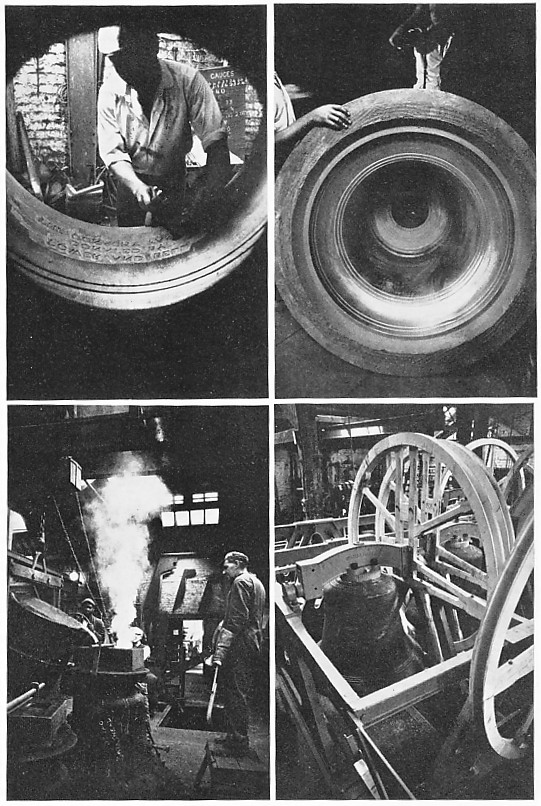
In the tuning process fine parings of metal are taken off with a lathe until the bell reaches the correct pitch. Instruments for checking tuning have now become so accurate that they are in fact inaccurate, as they can record a range of sounds beyond the human ear and they adjust to a scale which sounds perfect no doubt to ethereal ears but quite wrong to flesh and blood ones. In the final stages therefore, only human sounding boards are used.
The Whitechapel Bell Foundry also makes handbells, for which moulds of sand like little bell-shaped sandcastles are used for the core. In tuning bells of this size even the final polishing they are given can have an effect on the sound.
Every bell is made individually over a period of two or three months, If anything goes wrong, the whole process must begin again, with corresponding waste of time, money and labour. There are no short cuts. In such circumstances, skill is the very essence of the business.
One last request: please do not try to visit the foundry. They already have more visitors than they know what to do with and there is really not room for them in the high sheds, filled with Piranesi shadows and machinery, the floors covered with bells awaiting repair. Since the managers are too courteous to find it easy to drive people away, you might reflect that they have a two-year backlog of work and there are only two belles left in England. If to keep the belfries of the world reeling with changes, keep away and let them get on with it.